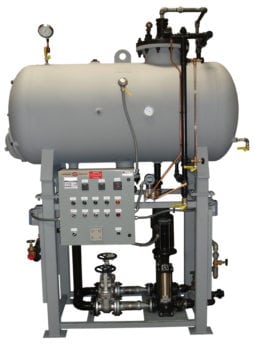
Never A Compromise For Quality or Safety
T Parker Deaerator incorporates a number of features, which make it unique on the market, more modern, with fewer moving parts, simpler and easier to operate. The unit provides a complete packaged assembly for easy field installation.
Tray & Spray
Feedwater Deaerators
Capacities 3,500 - 51,750 LBS/HR
Parker Deaerator Design
The Parker Deaerator design has been shown to reduce the residual oxygen level in make-up water to below 7ppb or .005cc per liter, CO2 is virtually zero.
Parker Deaerator Advantages
- Oxygen Removal to .005 cc/l (7ppb)
- CO2 Removal to virtually 0
- Reduced Boiler & System Corrosion
- Electronic Water Level & Pressure Control (No Mechanical Floats)
- Reduced Energy Cost of up to 14%
- Quick Start Scrubber Design
- ASME Code Vessel Construction
- Reduced Chemical Cost
- Standard 10 Minutes of Storage Capacity
- SS Internals
- Complete Packed Units
- Heavy Duty Stand
- Complete Line of Pump & Control Package Available
- Easy Access
The
Process Deaeration is the process of removing the dissolved oxygen from the boiler feed water. Additionally, in the deaeration process the CO2 is also removed. Removal of these two gases is important in boiler feed water as both of these gases promote corrosion in the boiler or steam system. An additional benefit of a deaerator is the conservation of flash steam in systems with large amounts of condensate return. This can result in substantial energy savings of up to 14%.
Operation
Deaerating is occurring in the Parker vessel via two separate actions. In the tray type (DAT), as the feed water enters the tray column from the top of the dome, it cascades down a series of trays and encounters a counter flow steam vent. This counter flow action removes oxygen and carbon dioxide. In the tank of the deaerator, there is a scrubber, which continually circulates the water in the deaerator bringing it in contact with steam and causing deaeration of this water. The spray type (DAS) uses a counter flow water spray over the venting steam. The scrubber action is identical on both designs.
Water Level Control
The water level control is based on an electronic water level sensor and controller, which generate a 4-20 milliamp signal to an electronic modulating make-up valve. The steam is controlled in a similar manner via a similar controller and is based on temperature in the vessel; this controls an electronic modulating steam make-up valve.